Sand casting is the most common casting
method employed in today's metal casting industry. Even
though much of the process has been automated, the practice
of sand casting is essentially unchanged from methods
used by early man. Simply put, metal is melted in a furnace
and then poured into a cavity/impression made in sand.
Precision Enterprises specializes in the sand casting of several types of aluminum (non-ferrous) alloys. This page defines some common terms used in our business.
Sand Casting Mold: A sand casting mold includes a top, bottom and a middle. A pattern, or impression device called a match plate, sits in the middle of the mold, and is surrounded with a sand/mineral mixture. The two halves of the mold are then separated and the match plate is removed. The two halves of the mold are then placed back together so that a cavity or impression is formed where the match plate was originally located.
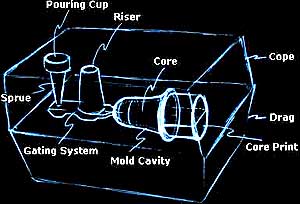
Green Sand: Sand used in sand casting (actually a naturally occurring mineral that is ground specially for this purpose) retains its form even after the impression device is removed. This ability is due to the extremely precise consistency of the sand mixture which is determined by a precise ratio of ingredients that include mineral, clay and a moistening agent. In the case of "green" sand (actually black in color) the moistening agent is water.
Mold Core: For cast parts that require a hollow chamber, an additional piece called a core is placed into the mold impression to prevent molten aluminum from filling that area. Cores are made from a special type of sand mixture that sets up relatively fast and hard but can be later removed by vibrating the cast piece and disintegrating the core so that it literally pours out of the cast part.
Automated Molding. An automated, or flaskless, molding machine uses the same principles described above, but automates the insertion of the match plate, the filling of the mold with sand, the compression and separation of the two halves (called the cope and drag) and the removal of the match plate. The machine then sends the prepared mold down a conveyor for pouring.
Pattern: A three-dimensional representation of the actual part being cast which is also sometimes used as the impression device located in the middle of a mold. Patterns can be made from plastic, hardwood, plaster or specialized polyurethane foams. They can be made by hand or using computer-controlled cutting machines or a rapid-prototyping process known as stereolithography.
Match Plate: In automated molding, the impression device that is used in the center of the mold. The Match plate is generally made from aluminum and is cast using a plaster mold created from the original pattern.
Flask assembly: The top and bottom of the mold which holds the entire configuration in place.
Cope: The upper or topmost section of the flask of the mold.
Drag: The bottom of the mold flask.